WE OFFER TURNKEY SOLUTIONS TO AUTOMATE PASSENGER VEHICLE DRIVING
IN FACTORY GROUNDS, VEHICLE LOGISTIC YARDS & PROVING GROUNDS.
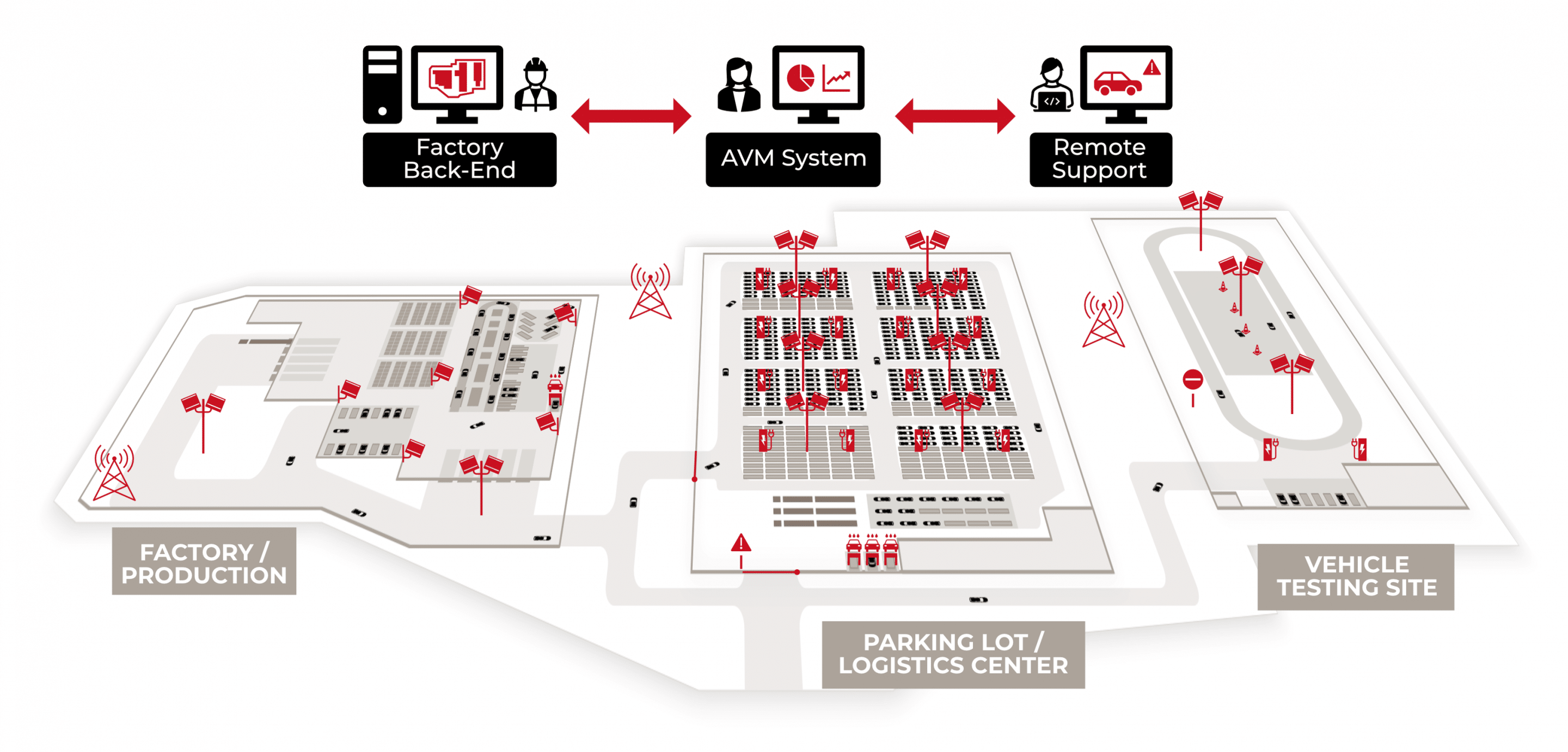
Embotech’s technology platform is powering the AVM solution and enables vehicles to maneuver safely, smoothly, and efficiently in real-time. Our AVM solution is infrastructure based in terms of sensing and compute, requires minimum intervention on the vehicle side and can coordinate multiple vehicles simultaneously.
World’s First AVM System in Production Facilities
COMPLIANT WITH ALL RELEVANT SAFETY STANDARDS
FOR AUTOMATED DRIVING WITHIN FACTORY GROUNDS AND VEHICLE LOGISTIC CENTERS – CERTIFIED BY TÜV SÜD.
Automated Vehicle Marshalling (AVM)
How?
Our AVM solution uses smart infrastructure to automate vehicle operation. This innovative approach minimizes the requirements on the vehicle itself, allowing us to control almost any standard production car.
Watch the video below for a deeper dive into how it works!
©BMW AG
Why it matters? The Impact of AVM
Current methods of manually driving vehicles through different stations of the production is costly and inefficient. AVM offers a range of advantages
Cost Reduction
Saves 1/2 of the driver’s costs & eliminates damages.
Replaces traditional conveyors.
Efficiency Improvement
Minimizes driver and vehicle travel times.
Eliminates human error, e.g. misplacement of vehicles.
Production Flexibility
Adapts to changing layouts, growing volumes and new use cases.
Time-to-market of new models/variants.
Use cases
Our solution covers all use cases to be found in automotive factories: Conveyor belt exit, Wheel Alignment, Body & Paint Inspection, Squeak and Rattle, Engine Test, Sensor Calibration, Drive to Logistics.
The AVM advantage: Why choose Embotech?
Our solution offers a wide range of advantages:
safety
Safety Certified System & CE Marked – designed for highest availability.
Live in a production environment with a German OEM since July 2022.
Capabilities
Fully flexible planning in real-time, can react on e.g. road or test rig closures.
Max speed 30 kph – co-existence with mixed traffic/human-driven vehicles.
Easily configurable for all vehicle models/sub-models.
Cost Efficiency
No special HW needed, all HW is off-the-shelf (OTS).
No changes required in the infrastructure apart from lidar placement.
Lidar placement supported by advanced tooling.
automated vehicle testing
How?
With Embotech’s proprietary technology, we use smart infrastructure to automate vehicle testing operations. Similar to AVM, the requirement on the vehicle are basic.
©BMW AG
Looking for more information?
If you’d like to find out more about our AVM Solutions, let us know. Either use the webform on the right or book a meeting via the link below. Our team of experts will be happy to discuss more details with you.